Der 3D-Druck erlebt seit Jahren ein Wachstum, wie wir es vergleichbar von der Chip-Entwicklung her kennen. Entstanden früher vor allem Prototypen und Neuentwicklungen mit der generativen Fertigung, so sind es heute auch schon Kleinserien.
Zu einem erfolgreichen Bauteil für den 3D-Druck gehören vier wichtige Säulen: eine Idee, die Konstruktion in CAD (in einer Kombination mit einer Software für die Konstruktion, die für den 3D-Druck optimiert ist), ein geeigneter Drucker und das passende Material. Wir wollen uns im Folgenden mit Letzterem, dem Material, beschäftigen.
Für das Druckverfahren von Kunststoffen wird, neben dem Filamentverfahren, in den meisten Fällen auf festen Werkstoff in Pulverform zurückgegriffen. Voraussetzung für eine hohe reproduzierbare Endqualität des Bauteils ist ein möglichst gleichmäßiger Schichtauftrag. Dies wiederum impliziert ein möglichst gut fließfähiges Schüttgut mit enger Kornverteilung.
Die Rheologie in Extrudern ist weitestgehend bekannt und kann als Vergleich für die Betrachtung eines Schüttgutes dienen. Dort werden hohe Dehn- und Schergefälle erzeugt. Diese Beanspruchungen führen zum Schmelzen des Kunststoffes. Über gezielte mechanische und thermische Maßnahmen im Extruder lässt sich eine gewünschte Viskosität des geschmolzenen Materials einstellen. Dabei ist ein hohes Maß an Materialkenntnis notwendig, um Oxidationsvorgänge zu vermeiden. Ein anderes Beispiel für die prozesssichere Nutzung der Rheologie sind Kunststoffgranulate (3 bis 5 mm), die als Aufgabe für Spritzgießmaschinen oder Folienblasextruder dienen.
Das rheologische Verhalten von Schüttgütern
Für einen verbesserten Schichtaufbau im Materialbett des Druckers ist das gleichmäßige „Nachrieseln“ des Granulats notwendig. Dies wird durch eine engere Kornverteilung erzielt. Im Vergleich zur Schmelzrheologie unterscheidet die Rheologie der Schüttgüter vor allem das „Gedächtnis“. Schüttgüter verhalten sich unter Last bis zur Fließgrenze elastisch. Unterhalb der Belastungsfließgrenze Verhalten sich Schüttgüter reversibel elastisch. Oberhalb der Fließgrenze kommt es zum gewünschten Fließen des Materials. Was hat es mit dem Gedächtnis auf sich? Ein verdichtetes Schüttgut hat eine höhere Fließgrenze – das Material hat die vorherige Belastung in sich gespeichert. Genutzt werden solche Effekte an Bahndämmen oder bei den Fundamenten im Hochbau. Abgelagertes Schüttgut in Säcken oder Big-Bags zeigt ähnliches Verhalten und stört somit eine gute Prozesssicherheit.
Die Rheologie der Schüttgüter wird von der inneren und äußeren Reibung beeinflusst. Die äußere Reibung ist das Zusammenwirken des Schüttgutes mit der Maschinenwand oder der Innenfläche eines Big-Bags. Die äußere Reibung ist in den meisten Fällen durch geeignete Werkstoffauswahl beherrschbar. Die innere Reibung hingegen wird von den Materialeigenschaften des Pulvers bestimmt. Es ist einsichtig, dass kugelförmige Körner weniger Reibung verursachen als kubische Partikel. Letztlich entscheidend ist die spezifische Oberfläche eines Pulvers und damit die Anzahl der Kontaktstellen zu den einzelnen Partikeln. Was ist damit gemeint?
Pulver für den 3D-Druck werden oft durch mechanische Zerkleinerung mithilfe von Kryogenmühlen in die gewünschte Feinheit gebracht. Die Mühle erzeugt im Normalfall durch die statistischen Effekte der Prallbeanspruchung eine stetige und breite Kornverteilung (siehe Bild 1).
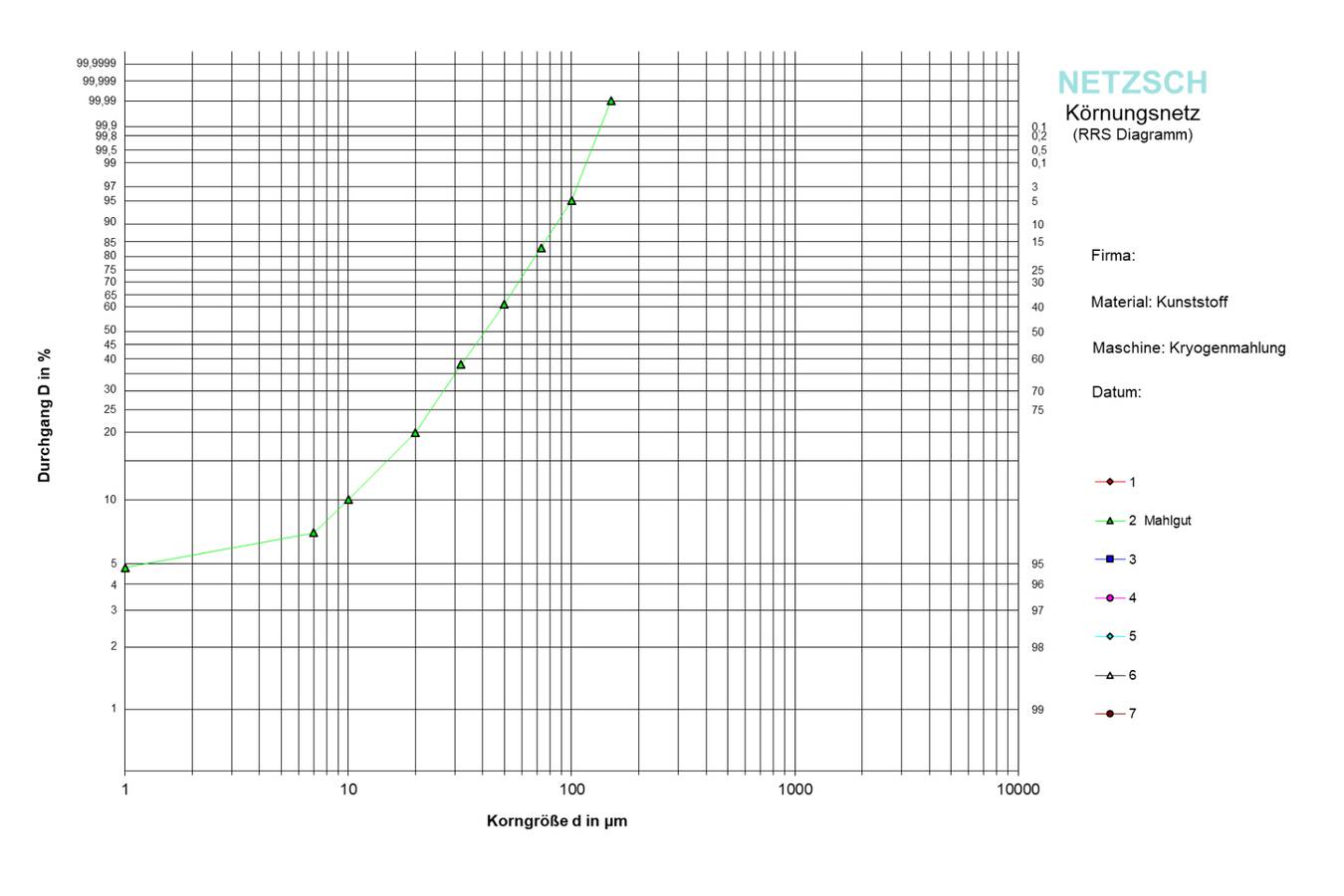
Bild 1: Kornverteilung eines Mahlgutes
Durch optimierte Prozessparameter kann die Kornverteilung etwas eingeschränkt und damit „enger“ gemacht werden. Allerdings kommen kleinere Partikel in der Anzahlverteilungskurve deutlich häufiger vor als Größere. Dies führt zu deutlich häufigeren Kontaktstellen zu anderen Körnern und erklärt somit vereinfacht das rheologische Verhalten von Schüttgütern. Das „Entfernen“ der kleineren Partikel hat somit deutlich mehr Einfluss auf die Kontaktanzahl.
Verbesserung des Fließverhaltens von Pulvern
Gemahlene Partikel liegen in kubischer oder irregulärer Form vor. Diese Formabweichung von der Kugelform erhöht die Kontaktanzahl und damit die innere Reibung.
Um nun das Fließverhalten von Pulvern zu verbessern, können zwei Wege eingeschlagen werden:
- Verrundung der kubischen Partikel
- Weitere Einengung der Kornverteilung
Bei der Verrundung werden durch mechanische Beanspruchung Kanten abgebrochen oder Partikel so verformt, dass eine kugelige Form angestrebt wird. Mit dieser Möglichkeit wollen wir uns hier aber nicht weiter beschäftigen.
Für den 3D-Druck werden Pulver < 150 µm eingesetzt. Beispielhaft ist in Bild 2 eine Kornverteilung einer Prallmühle als Ausgangsprodukt dargestellt. Hier kann der Feinanteil nur durch Sichtung entfernt werden. Klassische Siebmaschinen stoßen bei der Abtrennung von feinem Material < 300 µm an technische Grenzen. Nachteilig an den Siebmaschinen ist, dass sich während der Materialbewegung auf dem Siebdeck elektrostatische Aufladungen bilden können.

Bild 2: Kornverteilung eines Mahlgutes für 3D-Druck
Bei der Trennung mit Abweiserad-Sichtern wirken zwei einstellbare Kräfte auf die Partikel: die Zentrifugalkraft und die Schleppkraft der Sichtluft. Der Luftstrom wird üblicherweise von einem Ventilator erzeugt und durchströmt das Sichtergehäuse von außen nach innen. In den meisten Fällen werden die Partikel durch den Luftstrom dispergiert. Zusätzlich kann durch konstruktive Maßnahmen im Sichter die Dispergierwirkung verbessert werden. Der gesamte Luftstrom wird durch das rotierende Sichtrad hindurchgesaugt. Die Zentripetalkraft auf die Partikel durch das rotierende Sichtrad verhindert, dass zu grobes Material mit dem Luftstrom in das Innere des Sichtrades gelangen kann. Das feine Material verlässt das Sichtergehäuse mit dem Luftstrom und wird an einem Produktfilter vom Luftstrom getrennt.
In diesem Prozess ist das vom Feinanteil abgetrennte Material das Endprodukt – auch Grobgut genannt.
Der im Endprodukt verbliebene Feinanteil lässt sich je nach Anforderung im Druckprozess beziehungsweise nach wirtschaftlichen und physikalischen Gesichtspunkten einstellen. Da der Feinanteil nicht für den Druck verwendet werden kann, muss dieser dem Extruder zurückgeführt werden.
Der Messwert für den Grobgutanfall ist das Grobgutausbringen.
g = 1 - qf/qa
Dieser Wert beschreibt, wie viel vom Aufgabegut als Grobgut anfällt. Um die Sichteffizienz zu messen, wird die Tromp-Kurve verwendet:
Tg(x) = (g * qg(x)) / qa(x)
Die Tromp-Kurve beschreibt die Wahrscheinlichkeit, mit der ein Partikel eine bestimmen Korngröße (x) in die Grobgutfraktion verwiesen wird.
Abtrennung von Kunststoff
Die Qualität einer Sichtung wird mit der Steigung der Tromp-Kurve in den Punkten 25 und 75 % ermittelt. Bei einem Wert von 1 spricht man von idealer Trennung.
κ = x25/x75 = 18,45 µm/28,79 µm = 0,64
Technisch gute Sichtungen weisen einen κ-Wert von 0,6 bis 0,9 auf. Der beispielhafte κ-Wert bei einer Abtrennung von 50 µm ist für Kunststoff als sehr gut zu bewerten.
Wirtschaftlich von Bedeutung ist noch die spezifische Sichtenergie.
Espez. = (ESicht + EVentilator) / mg
Hier kommt es darauf an, die Antriebe gut auszulegen. Entscheidend dabei ist, dass die Anlagen- und Ventilatorkennlinie im optimalen Punkt betrieben werden. Weiteres Potenzial liegt im Ausreizen der frequenzgesteuerten Antriebe.
Zusammenfassung
Neben der mechanischen Verfahrenstechnik der Sichtung ist natürlich die Anlagentechnik in Bezug zu den Materialeigenschaften zu beurteilen. Die meisten Kunststoffpulver sind in der Staubexplosionsklasse St 1 beziehungsweise St 2 eingeordnet, andere wiederum dürfen nicht mit Luftfeuchtigkeit in Kontakt kommen.
Eine für unsere Mitarbeiter sichere Verarbeitung ist nur auf einer Atex-konformen, druckstoßfesten Sichtanlage und der Zulassung für die jeweiligen Staubklassen möglich.
Eine Verbesserung der Fließeigenschaften von Kunststoffpulvern für den 3D-Druck kann einerseits durch Abtrennen des Feinanteils mittels Sichtung vorgenommen und andererseits durch Einsatz verschiedener Mahltechnik in der Kornform erreicht werden.
Autor: Robert Rosen, Geschäftsführer, NETZSCH Lohnmahltechnik GmbH